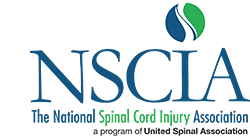
Job Information
TE Connectivity SR MANUFACTURING ENGINEER in HERMOSILLO SONORA, Mexico
SR MANUFACTURING ENGINEER
At TE, you will unleash your potential working with people from diverse backgrounds and industries to create a safer, sustainable and more connected world.
Job Overview
TE Connectivity's Manufacturing Engineering Teams are process leaders for stamping, molding or assembly related topics, ensuring the processes are running at optimum levels for quality and output. They are experts in mold tooling, die tooling, machining, and assembly techniques, possessing extensive knowledge of the associated manufacturing processes which may include the optimization and standardization of stamping / molding / assembly or other processes within the manufacturing environment. Manufacturing Engineering Teams enable the TE business unit plants to reach TE Operating Advantage (TEOA) requirements, roll out Centers of Excellence (COE), Best Demonstrated Practices (BDP’s) and advise plants on tool and machine duplications / corrections / improvements. They design and develop manufacturing process and automation platforms and apply them for the realization of new product developments as well as optimization of existing products already in production. The Teams also support Product Development in the selection and optimization of tools for piece part production and the selection of the most suitable manufacturing concepts relative to planned manufacturing quantities, quality requirements and manufacturing location. They act as interface between engineering and production to ensure manufacturability of new designs and smooth production ramp up as well as support the research & development teams to produce sample manufacturing equipment, product samples and prototypes.
Key Responsibilities
• Lean Manufacturing Implementation:
Lead the development and implementation of Lean Manufacturing strategies across the organization.
Conduct Value Stream Mapping (VSM) to identify and eliminate waste in processes.
Train and mentor employees on Lean principles, tools, and techniques.
• Process Improvement:
Analyze current manufacturing processes to identify areas for improvement.
Develop and implement process improvements to increase efficiency, reduce costs, and enhance product quality. Utilize Six Sigma methodologies to solve complex manufacturing problems and ensure process consistency.
• Project Management:
Manage and execute continuous improvement projects from conception through implementation.
Develop project plans, timelines, and budgets.
Monitor project progress and adjust plans as necessary to ensure successful completion.
• Data Analysis and Reporting:
Collect, analyze, and interpret data to drive decision-making.
Prepare detailed reports and present findings and recommendations to senior management.
Use statistical tools to analyze trends and identify root causes of issues.
• Cross-functional Collaboration:
Work closely with other departments (e.g., Production, Quality, Maintenance, Supply Chain) to ensure alignment and support for Lean initiatives.
Facilitate cross-functional team meetings and workshops to foster collaboration and continuous improvement.
• Compliance and Safety:
Ensure all process improvements and engineering changes comply with industry standards and regulations. Promote a culture of safety and ensure adherence to all safety protocols and procedures.
What your background should look like:
Education: Bachelor's degree in Industrial Engineering, Manufacturing Engineering, or a related field.
Experience: At least 5 years of experience in industrial engineering with a strong focus on Lean Manufacturing.
Proven experience in leading Lean transformations and continuous improvement initiatives.
Hands-on experience with Six Sigma and Lean implementation.
Technical Skills:
Proficiency in Lean Manufacturing tools and techniques (e.g., Kaizen, Kanban, VSM).
Strong analytical skills and experience with data analysis software (e.g., Minitab, Excel).
Knowledge of ERP systems and manufacturing execution systems (SAP).
Soft Skills:
Excellent leadership and team management skills.
Strong communication and interpersonal skills, with the ability to influence and engage stakeholders at all levels.
Strategic thinker with excellent problem-solving abilities.
Preferred Qualifications
Master's degree
Experience in automotive industry.
Black Belt certified.
Certified in Project Management (PMP or equivalent).
Valid Visa.
Location: Onsite.
Travel: 10%-25%
#LI-Onsite
Competencies
Values: Integrity, Accountability, Inclusion, Innovation, Teamwork
Location:
HERMOSILLO SONORA, SON, MX, 83118
City: HERMOSILLO SONORA
State: SON
Country/Region: MX
Travel: 10% to 25%
Requisition ID: 122488
Alternative Locations:
Function: Engineering & Technology
TE Connectivity and its subsidiaries, affiliates, and operating units (collectively, the "Company") is committed to providing a work environment that prohibits discrimination on the basis of age, color, disability, ethnicity, marital status, national origin, race, religion, gender, gender identity, sexual orientation, protected veteran status, disability or any other characteristics protected by applicable law or regulation.