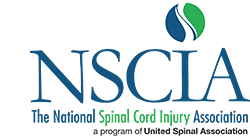
Job Information
Mesa Labs Manufacturing Operations Technician IV in Lakewood, Colorado
Description
Are you looking for an opportunity to make a difference? At Mesa Labs we're passionate about protecting the vulnerable by enabling scientific breakthroughs, ensuring product integrity, increasing patient and worker safety, and improving quality of life around the world. At Mesa Labs we offer competitive wages, including bonus opportunity, and a comprehensive benefits package.
Base Compensation Range: $25-28/hr This position is eligible for an annual 10% bonus opportunity in addition to the base salary
Outstanding Benefits and Perks: We are proud to offer a variety of benefits that meet the diverse needs of our employees: Eligible for benefits the first day of the month after you start Tiered Medical, Dental and Vision Insurance options Health savings (HSA), healthcare & dependent care flexible spending (FSA) accounts Company paid short term and long-term disability (unless covered by a state disability plan) Company paid life insurance and AD&D 3 weeks of accrued vacation time; accruals begin on Day 1 Paid sick leave of 48 hours per calendar year Eligible employees may receive four (4) weeks paid Care Giver leave after 1 year of service or in accordance with state leave laws 401(k) plan that provides a 4% Safe Harbor company match on a 4% employee contribution that begins on Day 1 Employee Wellness and Financial Assistance Resources through Cigna and NY Life Nine (9) paid company holidays per year Overtime opportunities This position supports our Calibration Solutions business. Our Calibration Solutions portfolio uses the principles of advanced metrology to enable customers to measure and calibrate critical parameters in applications such as Environmental and Process Monitoring, Dialysis, Gas Flow, Air Quality, and Torque Testing. Job Summary The Manufacturing Operations Technician IV is responsible for ensuring the overall efficiency, quality, and safety of manufacturing operations. This role requires advanced expertise in production systems, process optimization, equipment management, and team leadership. The Technician IV drives continuous improvement by implementing advanced technologies, troubleshooting complex issues, and mentoring junior staff. Additionally, they lead strategic initiatives to optimize manufacturing workflows, increase productivity, and uphold the highest standards of quality and safety. Duties/Responsibilities: Leadership and Strategic Oversight: * Lead and manage the daily operations of manufacturing processes, ensuring optimal performance, efficiency, and safety across multiple production lines. * Serve as a subject matter expert (SME) and provide technical leadership to the manufacturing team, offering guidance on complex issues related to equipment, processes, and safety. * Develop and implement long-term strategies for improving manufacturing processes, including the adoption of new technologies and best practices. * Provide mentorship and training to junior technicians, fostering their development and ensuring the team operates at the highest standards. Process Optimization and Continuous Improvement: * Spearhead the identification, design, and implementation of advanced process improvements to optimize efficiency, reduce downtime, and eliminate waste using Lean, Six Sigma, or other continuous improvement methodol * Lead high-impact projects focused on improving productivity, cycle time, and quality, while achieving cost reductions and operational efficiencies. * Use advanced data analysis and performance metrics to evaluate processes, equipment, and production outcomes, providing actionable insights for improvement. Troubleshooting and Root Cause Analysis: * Lead the troubleshooting and resolution of complex equipment issues, production bottlenecks, and process inefficiencies that require advanced technical knowledge and problem-solving abilities. * Perform root cause analysis (RCA) for equipment failures, qual ty issues, and production disruptions, implementing corrective and preventive actions to mitigate future occurrences. * Oversee the repair and maintenance of critical manufacturing equipment, working with cross-functional teams to ensure quick turnaround times and minimal downtime. Advanced Equipment and Technology Management: * Oversee the maintenance, calibration, and optimization of advanced manufacturing equipment, including automated systems, CNC machines, robotics, and other high-tech machinery. * Drive the integration of new technologies and automation tools to improve production capabilities, product quality, and process control. * Evaluate and recommend new equipment, tools, and technologies that align with the company's long-term operational goals. Quality Assurance and Compliance: * Ensure adherence to strict quality standards by monitoring production outputs, performing advanced inspections, and managing quality control processes. * Lead efforts to improve product quality, reduce defects, and maintain compliance with internal and external quality standards, including ISO, GMP, and regulatory requirements. * Work closely with the quality control team to perform audits, identify deviations, and implement corrective actions to address any quality concerns. Health, Safety, and Environmental Leadership: * Champion safety initiatives and ensure full compliance with OSHA regulations, environmental policies, and company safety standards. * Lead safety audits, inspections, and hazard assessments, ensuring that all operations adhere to the highest safety standards. * Investigate incidents, accidents, and near misses to determine root