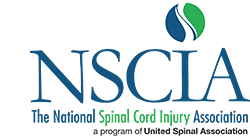
Job Information
Terex Corporation Production Control Coordinator in Moses Lake, Washington
Job Description: Overview: Ensures that material flow within production environment is on time and maintains delivery standards as set-forth in the Terex Production System and Terex Materials Management System. Maintains and facilitates timely order and delivery of parts, components, and supplies to support areas such as production and parts service. Provides a communication and logistics link between planning, inventory, engineering and purchasing. Responsible for scheduling production areas and communicating all variances with concerned parties. Main Duties & Responsibilities Actively participate in DMS including VS and Materials Tier 2 and 3 meetings. Schedules and coordinates all activities related to reschedules, ECO changes, conversions and options. Prepare reports summarizing production and supply related information (supply variances, downtime, manufacturing quality issues) Establish and maintain all line side inventory including set up, set inventory levels, monitor (and correct) integrity of racking, location maintenance. Coordinate, create, and maintain all production and withdraw kanbans - cards/racks/carts for the value stream in your assignment. Calculating/maintaining minimal SWIP levels necessary to support Production kanban. PFEP pick list dispatch and maintenance. Create and status project requests for new or replacement carts/racks when needed to support SWIP levels. Identifies and communicates all potential and real schedule variance for on-time delivery to the customer. Acts as primary liaison between departments, facilitating on time delivery of materials, parts and supplies. Identifies and resolves daily material issues, facilitating or ordering necessary parts, components, and supplies for production. Assists Kanban Coordinators, Buyers/Planners and other Materials support team to develop, interpret, and convert intermediate-term plans into action plans. Coordinates daily workflow between manufacturing teams to ensure needed supply to the line and internal customer for continual flow. Reviews master production schedules, confers with Materials Team Members, and serves as liaison between all other departments to facilitate material flow. Communicates daily priorities to manufacturing teams, coordinating materials from vendors as necessary. Maintains variance tracking and kaizen newspaper detailing continuous improvement action items with a specific focus on safety, delivery, quality and cost. Reports progress on activities. Ensures a safe and healthy work environment through compliance to HR and Safety policies and procedures. Establishes and maintains positive working relationships with all customers. Performs other duties as assigned. Required Qualifications: Employee must be self-motivated with the ability to work independently and in a team environment. Excellent communication skills - verbal, written and presentation. Highly capable in problem solving, prioritizing and multi-tasking techniques. Working knowledge of ERP, Production Planning, MRP, Kanban, Lean Manufacturing and Inventory Control. Working knowledge of MS Office - Word, Excel (macros), Outlook, PowerPoint Minimum of 4 years of experience in a manufacturing environment Experience and/or training in Lean Manufacturing, Process Improvement Ability to work well under pressure Knowledge and understanding of manufacturing assembly processes High School Diploma or Accredited GED Strong orientation toward quality, safety and continuous improvement Preferred Knowledge, Skills and Abilities: 1+ year of leadership experience 1+ year experience with ECO Implementation New product implementation Some collegeor technical education is a plus. Working with Kanban a plus Related technical ability and good understanding of production processes and equipment Demonstrated leadership ability, includ