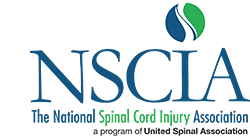
Job Information
Dairy Farmers of America QA Compliance Foreman in Turlock, California
Position : QA Compliance Foreman
Location : Turlock, California
Requisition ID: : 26864
Schedule: Tuesday to Saturday - 9:00am - 5:30 pm
Days Off: Sunday & Monday
(Schedule is Subject to Change)
General Purpose:
Assist the facility staff to maintain Quality Assurance and Food Safety Programs in compliance with all DFA policies, procedures, customer specifications, and regulatory requirements. Responsible for a variety of document review functions. Participate as a member of the Food Safety (HACCP) team. Deliver training to team members. Support the laboratory, be familiar with the laboratory testing procedures, and occasionally act as a backup in the lab department. Conduct quality assurance and other compliance inspections as needed.
Job Duties and Responsibilities:
Assist management to ensure daily plant operations for Quality, Food Safety, and Personnel Safety are following DFA policies, procedures, customer requirements, as well as local, state, and federal regulations
Participate as a Food Safety and Quality team member
Perform daily record review of all CCP-related documents (HTST charts, metal detector logs, etc.) and document findings
Escalate non-conformance events to the proper QA and operations personnel
Assist with annual review of the Food Safety (HACCP) program and associated documents
Coordinate training for plant employees to meet requirements for FSMA/HACCP
Create or review documents and policy statements to meet assigned sections of SQF or other standards
Obtain and maintain CIS status for PMO Appendix N antibiotic testing program
Coordinate vendor compliance
Complete evaluation of all incoming ingredients and packaging materials following the “Hold and Release” program, including review of Certificates of Analysis, comparison to specifications, and release in SAP
Work with DFA corporate staff to ensure all necessary documentation is on file from vendors to meet customer and DFA requirements and is kept current (Kosher certificates, Halal certificates, Letters of Guarantee, Statement of Origin, Allergen Statements, etc.)
Function as a backup to lab tech and lab lead
Maintain familiarity with and perform all duties and responsibilities as described for general lab tech
Perform laboratory tests (chemical, physical, organoleptic, and microbiological) according to prescribed standards on in-process, finished food products, and ingredients
Determine compliance to specifications
Communicate results to Fore people and other staff
Develop working knowledge of other lab duties, including EMP/PEM/HEM swabbing, equipment calibration, and basic maintenance/troubleshooting
Perform lead tasks (equipment calibration, lab inventory management, glass inspection, equipment troubleshooting, etc.) as assigned
Provide training
Facilitate scheduling and/or delivery of quality/food safety training to plant employees, visitors, and service contractors to meet corporate and regulatory requirements
Develop and deliver short “Quality Topics” and other training
Ensure training effectiveness and comprehension, revise/update training material as needed
Provide monthly progress reports to the QA Manager
Participate in audits
Actively participate in plant internal audits, pre-start inspections and other audits as assigned
Document findings and generate reports to be distributed to cross-functional teams for corrective actions
Coordinate document preparations and review for audits and inspections (customer, third-party, DFA, or regulatory) as assigned
Assist QA management staff
Conduct investigations into incidents and quality issues; assist with product evaluations
Generate Quality Assurance reports from meetings, inspections, and service provider reports (pest control, sanitation, complaints, etc.), including trending and charting as appropriate
Coordinate Corrective Action Plans and distribute to staff in a timely manner
Coordinate Repacks with production supervisors
Organize all quality and production records in a clear and orderly manner so that they are readily accessible to QA staff. Ensure all records are accounted for in a timely manner
Utilize SAP
Navigate SAP and learn Tcodes for completing common transactions
Requests for purchase requisitions
Work requests via SAP for plant repair work
Hold and release activities in SAP, including data entry, spec review, and blocked stock transactions
Lot traceability and mock recall
Coordinate Label Review program for finished product labels and weight labels
Standardized Operating Procedures (SOP’s) and Sanitation Standardized Operating Procedures (SSOP’s)
Ensure plant personnel have access to the most recent versions of the Corporate Standardized SOP’s and plant SOP’s and SSOP’s and that all training records are current
Maintain a matrix chart by job description at the plant which indicates which SOP’s are applicable by job description
Prepare plant specific versions of SOP’s as needed for the plant
Ensure all forms and work instructions are linked to the plant SOP’s and coordinate the review, revision, and updated annually
Utilize Intelex to manage document/SOP annual review and revisions
Participate in continuous improvement programs, safety, and department 5S
Maintain current knowledge through seminars and industry publications to develop skills and improve job performance. Attend required training, including but not limited to Safety, GMP, HACCP, FSMA and Safe Quality Foods (SQF).
The requirements herein are intended to describe the general nature and level of work performed by employee, but is not a complete list of responsibilities, duties, and skills required. Other duties may be assigned as required.
PAY
Competitive pay - $25.65 to $31.48 per hour based on experience
Rate includes $1.00 shift differential for hours worked between 6 PM and 6 AM
Paid Overtime
BENEFITS
Medical
Dental
Vision
401k Employer Match
Life Insurance – Company Paid
AD&D, STD and LTD - Company Paid
144 hours of Paid Vacation
Paid Holidays
Paid Sick Time
Minimum Requirements:
Education and Experience
High school graduate or equivalent
Associate degree or equivalent course work preferred
2 years of experience in food processing environment or food lab
Certification and/or Licenses (must have or be able to obtain within 120 days or as agreed) –
HACCP/ Food Manager certification
SQF Practitioner certified
May be required to obtain and maintain other certifications and/or licenses in the future (PCQI certification, Appendix N CIS, etc.)
Knowledge, Skills and Abilities
Able to communicate clearly and effectively, both verbally and in writing, and to speak in front of large groups and lead employee education classes successfully
Able to work in collaboration effectively and foster good teamwork
Critical thinker, able to take appropriate steps to find solutions to problems
Able to organize and prioritize resources to achieve goals; able to keep organized records; able to work with accuracy and attention to detail is crucial to success
Knowledge of Microsoft Office Suite and company computer systems, specifically Excel, Word and SAP
Able to complete basic arithmetic in all units of measure using whole numbers, common fractions, and decimals
Able to demonstrate knowledge of basic microbiology
Able to adapt and manage to change effectively
Able to take initiative in performing a job without direct supervision
Able to type minimum 30 wpm
Able to work multiple shifts, weekends, holidays
Must be able to read, write, and speak English. Fluency in Spanish is a plus