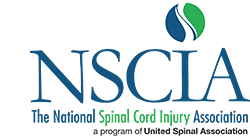
Job Information
Magna Process Technician - Blanking/Rolling in Vaughan, Ontario
Process Technician - Blanking/Rolling
Job Number: 67130
Group: Magna Exteriors
Division: Rollstamp Manufacturing (Snidercroft)
Job Type: Permanent/Regular
Location:
Vaughan, ONTARIO, CA, L4H 0S9
Work Style:
Job Number: 67130
Group: Magna Exteriors
Division : Rollstamp Manufacturing (Snidercroft)
Job Type: Permanent/Regular
Location: VAUGHAN
Work Style:
About us
We see a future where everyone can live and move without limitations. That’s why we are developing technologies, systems and concepts that make vehicles safer and cleaner, while serving our communities, the planet and, above all, people.
Forward. For all.
Group Summary
The Magna Exteriors portfolio of products includes access systems such as liftgates, exterior trim, modular systems, front-end modules including fascia, active aerodynamic systems and other lightweight structural components for automotive, commercial truck and other industrial markets.
Recognized globally as an innovator in all aspects of vehicle exteriors, Magna provides everything needed, from materials development and design through manufacturing and assembly, to help automakers create sleek, state-of-the-art vehicles across the world.
About the Role
• The Process Technician – Blanking/Rolling reports to the Operations Manager and is responsible for providing day-to-day assistance to the Operations Manager.
Your Responsibilities
• Monitor daily Production performance to ensure all cells meet the daily departmental goals and targets.
• Set up or assist in setting up of rolling mill tooling and material, testing and adjusting guides, fixtures and other aspects of workstation, until it is production ready.
• Conduct test runs and measurements to ensure pieces and parts produced meet required specifications.
• Audit daily first and last off approvals.
• Champion regular meetings with cross-functional teams to address and resolve issues affecting Department’s performance.
a) Reports any abnormalities of parts or machine to the Supervisor immediately. Suggest corrective action where applicable.
• Troubleshoot and problem solve of production line.
• Develop process specifications and operating conditions for new programs and implementing.
• Develop, conduct and document tests for new products and new material.
• Identify and incorporate ways to improve quality of parts.
• Support and execute engineering projects.
• Optimize current processes to improve efficiency, quality or cost reduction.
• Participate in Continuous Improvement programs to reduce cost.
• Encourage personal development and help operators to be trained.
• Lead the team by example: 5S, running the rolling mill, quality and inspection, rolling mill set up function (cross-functionality); use positive reinforcement rather than negative.
• Maximize Rolling Mill uptime by working with the Production Team to optimize the following:
a) Change-over downtime
b) Sweep and x-section adjustments during production run
c) Coil change downtime
d) Coolant filter change downtime
• Champion the development of all new sections:
a) Work with the various internal departments and roll forming suppliers to develop new cross sections
b) Maintain a documented portfolio of all development work done.
c) Develop Standardized Work Instructions (SWI) for the setup, running, packaging, labelling and layout of all new programs
d) Train Production staff to setup and run all new programs
e) Prepare department to achieve successful Run @ Rate runs
• Work with the Engineering Department to develop effective check gauges (ie. acceptable GR&R and can provide variable data where needed).
• Setup and maintain system to monitor cleanliness and viscosity of coolant.
• Train employees in the department to perform their duties to standard.
• Work with the Tooling and Maintenance Departments to ensure all tools and equipment are properly maintained and running optimally.
• Conduct audits regularly to ensure all systems (including 5S) are sustained.
• Responsible for proper storage, handling, and disposal of all chemicals, used materials and equipment.
• Comply with Section 28 of the OHSA.
• Comply with all Rollstamp Health and Safety policies and procedures.
• Comply with all Rollstamp IATF 16949 policies and procedures.
• Comply with all Rollstamp ISO14001 policies and procedures.
• Perform any other reasonable request by management.
Who we are looking for
Your preferred qualifications
Educational Requirements: Grade 12 or equivalent
Minimum Experience: Minimum 3 yrs hands-on working experience in a technical role in manufacturing; experience as rolling mill operator would be an asset.
Computer Skills: knowledge of MS Office applications, database management.
Communication Skills: Good oral and written skills, strong understanding of English language.
Additional Education/Experience/Skills:
• Excellent attendance record.
• Able to work in a team environment.
• Able to work with minimal supervision and be self-motivated.
• Excellent knowledge and understanding of quality requirements and specifications.
• Hands-on approach to problem solving.
• Good understanding of a roll forming process and part sweeping.
• Good understanding of SPC and ability to distinguish product conformance based on standards.
• Technically competent to perform the duties of a Set Up Operator.
• Ability to judge conformance or parts to specifications.
• Die set-up / rolling mill set-up.
• Forklift safety.
• Analyze defects, gather information, diagnose problems and make decisions.
• Able to work flexible shifts and overtime when required.
What we offer
At Magna, you can expect an engaging and dynamic environment where you can help to develop industry-leading automotive technologies. We invest in our employees, providing them with the support and resources they need to succeed. As a member of our global team, you can expect exciting, varied responsibilities as well as a wide range of development prospects. Because we believe that your career path should be as unique as you are.
Site Benefits
Awareness. Unity. Empowerment.
At Magna, we believe that a diverse workforce is critical to our success. That’s why we are proud to be an equal opportunity employer. We hire on the basis of experience and qualifications, and in consideration of job requirements, regardless of, in particular, color, ancestry, religion, gender, origin, sexual orientation, age, citizenship, marital status, disability or gender identity. Magna takes the privacy of your personal information seriously. We discourage you from sending applications via email to comply with GDPR requirements and your local Data Privacy Law.