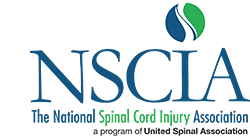
Job Information
TOLMAR Inc. Manufacturing Operator I - Packaging in Windsor, Colorado
Core Hours: Monday - Friday, 2pm - 10:30pm
Purpose and Scope The Manufacturing Operator I - Packaging is responsible for the full set up and safe, clean, efficient and consistent operation of inspection and packaging equipment and all associated documentation for all Tolmar products. They provide manual assistance to the team using automated and manual equipment while ensuring that products are made with quality for our patients.
Key Responsibilities Perform job responsibilities in accordance with standard operating procedures (SOPs) and production records with an expectation of "Right the First Time". Record data in notebooks or lab forms and accurately calculate results to support process. Perform job in a clean room environment requiring clean room gowning, including but not limited to: Company-provided Scrubs Shoe Covers Hairnets (and beard covers as applicable) Tyvek Coveralls Gloves Face mask Set-up, operate and monitor semi-automatic packaging equipment used to package pre-filled syringes. Automated packaging equipment includes (but is not limited to): semi-automated inspection, thermoformer, syringe connecting, labeler/vision systems, cartoning & serialization. Properly load pre-filled syringes and components into automatic packaging equipment. Interface with human machine interface (HMI) on automated equipment. Accurately document production activities using regulatory controlled documents including production records and log books. Correctly perform inspections of packaged components. Perform facility cleaning of manufacturing areas as required to maintain a cGMP environment and in accordance with Standard Operating Procedures. Properly perform job duties as a second-checker, ensuring all production activities are correctly performed per batch production records. Qualify and maintain 100% inspections of pre-filled syringes. Responsible for assembly, disassembly and sanitation of various equipment. Ensure that product quality adheres to approved specifications. Perform visual and physical checks of in-process and finished product as requested. Train new manufacturing employees to perform manufacturing processes. Conduct routine cleaning and monitoring of classified areas. Operate under the consistent supervision of a Lead Operator and/or Production Supervisor. Participate in required annual hazardous waste training. Hazardous waste involvement may include, but is not limited to container and tank management and inspections, generation of hazardous waste as a part of production or sampling processes and transfer of hazardous waste between lab procedure area, satellite accumulation and storage. Respond to spills per the Chemical Spill Procedures. Perform other duties as assigned.
Special Skills and Knowledge Working knowledge of current Good Manufacturing Procedures (cGMP). Ability to stand for extended periods of time (up to 8 hours or more). Working knowledge of basic computer software. Demonstrated ability to operate machinery. Ability to maintain focus on detail-oriented, repetitive tasks. Ability to follow and understand written production records and validation protocols. Understanding of basic math and writing skills to document production activities in batch records and/or log books. Must be able to keep accurate records and able to perform mathematical calculations. Ability to legibly complete required documentation. Strong attention to detail for documentation in production documents and to inspect produced goods within specified requirements. Capability to operate on a fast-paced manual assembly line using basic production equipment.
Core Values The Manufacturing Operator I - Packaging is expected to operate within the framework of Tolmar's Core Values: Center on People: We commit to support the well-being of our patients. We are committed to treating our employees and those we serve as valued partners. By placing people at the h art of our actions, we actively engage, invigorate, acquire knowledge, and grow together. Are Proactive & Agile: We embody a culture of engagement and action. With a hands-on approach, we fearlessly adapt to change. We anticipate, respond swiftly and efficiently to ignite a spirit that propels us towards extraordinary outcomes. Act Ethically: We are committed to consistently conducting our business in an ethical, compliant, and socially aware manner, in line with our purpose of positively impacting lives. We actively cultivate diversity, equity, inclusion & sustainability in our workplace. Constantly Improve: We are committed to a collaborative & proactive effort to improve our products, systems, processes, and services by reducing waste, increasing efficiency & improving quality. Are Accountable: We think, act, and communicate with honesty, transparency, and clarity in alignment with our core values. We don't compromise our values for near term gain. We take accountability & ownership of our work, actions, successes, and setbacks. We strive to deliver our best as we shape the future.
Communication Interact with peers and members of other departments in team settings in a professional manner.
Education & Experience