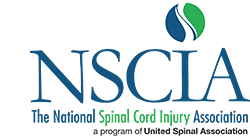
Job Information
Skookum Aerospace Manufacturing Quality Assurance Manager in Woodmont Beach, Washington
Quality Assurance Manager Location: Kent, Washington Type: Exempt Work Schedule: Full-time, Day Shift Compensation: $68,000 - $110,000 Annual Salary, Dependent on experience Benefits: Skookum is proud to offer a comprehensive compensation and benefits package to our eligible part-time and full-time employees. Medical, Dental, Vision, Life & Short-Term Disability Insurance Elective 401(k) retirement plan with up to a 3% employer match after 90-days of employment Flexible Spending Accounts for both medical and dependent care 11 paid federal holidays, accrual of 12 paid days of vacation at the start of employment, paid sick leave Potential shared earning bonus Tuition assistance is available after 1 year of employment and potential scholarships for qualified dependents Professional development, certifications, and training opportunities Verizon wireless discount Employee Assistance Program (EAP), and an engaging wellness program Public Service Loan Forgiveness eligibility for full-time employees Skookum Manufacturing is dedicated to serving the aerospace industry and has a long history of quality and excellent customer service. In 2023 the company is actively working to broaden the variety of products and components both developed and manufactured within its bounds. Skookum is seeking a reliable and motivated Quality Assurance Manager with a professional attitude. The Quality Assurance Manager will focus on creating and maintaining quality systems, policies, procedures, control process sampling systems, statistical techniques that meet or exceed Skookum Aerospace/customer requirements. Typical duties include but are not limited to: Clear understanding of AS9100/ISO9001 standard applicability to manufacturing processes and system compliance to standard. Development of Control Plans, Detailed Inspection Plans, failure modes and effects analysis (FMEA), QA Inspection and Test plans Manage Quality aspects of product launch and Production Readiness Reviews. Develop Inspection Acceptance criteria based on Skookum's / customer requirements and Key & Critical Characteristics Supports/leads production material review board (MRB) process and underlying cause of non-conformance Performs quality management system audits at supplier facilities as required Coordinates corrective action requests and other quality issues from customers Understands and ensures product traceability requirements are met Works closely with Product Engineering, Manufacturing Engineering and Customer in support of Continuous Improvement programs and projects Responsible for product and data presentation for final customer acceptance, Source Inspection, first article inspection (FAI), problem reporting and resolution (PRR), etc. Technical writing skills to develop quality procedures/test plans and communicate effectiveness of quality system Manage all aspects of Quality Assurance (QA) and Quality Management System ensuring that products meet regulatory, government and company compliance requirements. Managing all aspects of QMS activities while ensuring that systems and products are furnished in compliance with contractual quality requirements and design specifications. Reviews customer purchase orders to ensure that quality requirements are understood and flowed down to internal documents and supplier purchase orders Works with supplier group to add new suppliers and evaluate supplier performance including quality and on time delivery. Experience in data analysis (Cost of Quality, Nonconformance Trends, Scrap and Rework) reports and charts. Establish and lead a comprehensive Internal Audit program to cover International Standards (ISO 9001, AS9100) internal processes and procedures, customer, and regulatory agency require